Scarcity is a basic economic problem: people have unlimited wants and needs, but the world has limited resources. Resources in that equation include materials, capital, and labor. A pasta factory in southern Italy faced a very particular sort of labor shortage. The Barilla pasta factory in Foggia, Italy had enough employees to keep up with production schedules, but the employees weren’t showing up to work. The absentee rate among workers threatened the survival of the plant. Listen to the story to learn how bosses and managers changed employees’ attitudes and behavior and solved their scarcity issue.
Listen to the story
MELISSA BLOCK: This is ALL THINGS CONSIDERED from NPR News, I’m Melissa Block. This week, our Planet Money team has been reporting from the borders that divide Europe, and today we visit an unofficial dividing line between northern and southern Italy.
To many, the two might as well be different countries. The north of Italy has more industry and produces more goods; the south has higher unemployment and more corruption. Even within a single company, economists have found that employees in southern Italy don’t work as hard as their northern colleagues.
Well, our Planet Money team introduces us now to a pasta company that refused to accept this great divide and did something about it.
ROBERT SMITH: I’m Robert Smith in northern Italy, and I’m getting off the train in the town of Parma. Now, Parma’s known for its amazing food: Parmesan cheese, Parma ham, better known as prosciutto. But I’m here for a certain kind of pasta. It’s here, close to the wheat fields, that the Barilla family built the largest pasta factory in the world.
(SOUNDBITE OF MACHINERY)
SMITH: The building is huge. It’s the size of something like 100 soccer fields. Inside, it looks like a nuclear power plant – all buttons and pipes, guys in white lab coats. The plant manager shows me around.
UNIDENTIFIED MAN 1: In this moment, we are packaging the Spaghetti Number 5.
SMITH: Those familiar blue spaghetti boxes with bionic conveyor belts. Now, pasta is a cheap product. The way a company makes money is by making a lot of it quickly. One worker can run a machine that makes more than five tons of past an hour. So it’s really important that he shows up to work.
UNIDENTIFIED MAN 1: The man is absolutely very, very important.
SMITH: Each man is so important, in fact, that if even a couple of them don’t show up for work, it can shut down the entire plant, which is what happened at another Barilla pasta factory down south in the heel of Italy, 400 miles south of here.
ZOE CHACE: I’m Zoe Chace, just outside the Barilla plant in Foggia, in the south of Italy, and it’s a beautiful day. The sun is shining, the wind is blowing. Who would want to work on a day like today? And it turns out that’s exactly the problem the Barilla plant in Foggia was having, a lot of people weren’t showing up for work.
SMITH: And believe me, they noticed up here at the plant headquarters in Parma. The plant in Foggia had a very high absentee rate, 10, 11 percent. The Foggia plant was not producing their allotment of pasta.
CHACE: Nicola Calandrea is the plant manager down here, and he remembers people calling in sick constantly, usually on a Monday.
NICOLA CALANDREA: Or during football matches or around important holidays.
CHACE: Remember, one guy runs an entire factory line of capellini, and if that guy was out watching soccer…
CALANDREA: We had to stop.
SMITH: It costs a lot of money to run a pasta plant that’s not making pasta. So the headquarters up north sent one of the big bosses, Carlo Carteri(ph), down south with a message.
CARLO CARTERI: OK, guy, if you don’t want to work, there is no problem. I take this line in a place where people want work more than you. Or we change our approach all together, or this place probably in the future will disappear.
CHACE: So, Calandrea the plant manager down south, he heard this and he had to act. To save the factory, he had to change the entire culture.
SMITH: Calandrea is a southern Italian. He’s a trained scientist. To him it doesn’t make any sense that just being in the south would make you more of a slacker. He looked at the problem scientifically.
CHACE: He started out by meeting with the worst offenders, people who were sick…
CALANDREA: One day, two days every week.
SMITH: And Calandrea had a theory: People were calling in sick because they figured they could get away with it, that nobody noticed. So step number one, make the workers understand, hey, we see you, we notice.
CHACE: Calandrea met with each worker, said hi, I noticed you’ve been out sick a lot. When workers responded with notes from their doctor, Calandrea sent his own doctor to the workers’ houses to check up on them.
CALANDREA: It was a big surprise to hear a knock at the door and it’s the doctor.
CHACE: And then he took this masterstroke: He crafted a letter that said simply, here are the people who are absent most often, here are the doctors who are signing these notes. Then he sent that letter to the actual doctors and the professional organizations that they belong to.
CALANDREA: We wanted only to inform, to give the information to interrupt the problem.
SMITH: Calandrea took one other big step. He let everyone in the plant know what he himself knew, that absenteeism was a huge problem, worse in the south than in the north, and it was threatening the very survival of the factory.
CHACE: Michael Bineze is a worker at the plant. He makes bow-tie pasta. He says he was never one to call in sick, but all of a sudden even the workers with perfect attendance were freaked out.
MICHAEL BINEZE: (Through translation) We look at each other, and we know that we have to put some pressure on that other person, like to say, oh, you should come to work.
SMITH: Beneze remembers the moment he realized that the culture was shifting. It was an episode with another worker, Marco Tutti(ph).
BINEZE: (Through translation) He asked for a holiday, but the supervisor refused him because they needed him to work. So he said, at that point he called in sick.
CHACE: With a doctor’s note, of course, but Marco Tutti was not sick. Marco Tutti was playing soccer for a big local soccer team.
BINEZE: (Through translation) What was not good for him was that he went to play, but he also scored a goal.
(LAUGHTER)
CHACE: Tutti’s achievement was written about in the newspaper, and his fellow workers, instead of protecting him, they brought the paper to Calandrea, the plant manager.
SMITH: They ratted him out.
CALANDREA: Yes, because the sensitivity of people was increasing. They knew that the behavior of one of us could compromise the life of everyone.
SMITH: And so Calandrea fired Marco Tutti, and he gets very serious when he talks about this because it’s the only person he had to let go during this whole process. It’s very rare in Italy to be fired.
CHACE: It really sent the message home, though, and right after that, no surprise, the numbers started to improve here in Foggia. The absentee rate has dropped all the way from 10 percent to less than four percent. It’s a huge difference in just a couple years.
CALANDREA: Yes, good, but I think that we can improve it.
SMITH: It’s going to be tough for the absentee numbers to get much lower. In fact, the plant in Foggia is already doing better than the plant up here in Parma, Italy. I’m Robert Smith, and down south…
CHACE: Zoe Chace, NPR News.
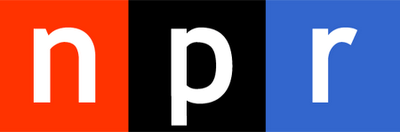
Vocabulary
- absentee rate – the percentage of people who are absent each day from a school or company
- culture – shared attitudes, values, goals, and practices that characterize an institution or organization
- master stroke – an outstandingly skillful act
- plant – a place where an industrial or manufacturing process takes place
- unemployment – the percentage of individuals within a given segment of the population who are able to work but lack a job
Listening Comprehension Questions
- What is the problem in this story?
- Why are individual workers so important in the Foggia plant?
- What was the outlook for the future of the Foggia plant?
- What steps did the manager take to reduce the absentee rate?
- How did the manager “interrupt” the problem of false doctors’ notes?
Discussion Themes
- How do you think employees rationalized their frequent absences?
- What other circumstances might create labor scarcity?
Teacher’s Guide
Activate student knowledge: Prompt a discussion about school attendance and the effects of student absenteeism. Then shift the discussion to work attendance and absenteeism. What are the economic factors that come into play when the focus shifts to the workplace? Who is affected when employees miss work?
Introduce the story: This story concerns a Barilla pasta factory in southern Italy that faced such a high employee absentee rate, its future was threatened. Listen to the story to learn how manager Nicola Calandrea addressed the problem and how workers responded. As you listen, make connections between this story and what you know about scarcity.
Active listening supports: Choose one of the following listening organizers to support student understanding as they listen to the story.
- The T-Chart: Problem and Solutions will guide student listening as they take notes on the absentee problem in the Barilla factory and the solution. For example, students might list the problem as: the factory is not producing enough pasta, and the steps taken as: Manager meets with worst offenders to show that he notices their absence, peer pressure, workers are told the survival of the factory was threatened by rate of absenteeism.
- The Language Identification organizer allows students to follow along and track important phrases while listening to the story.
Paired Text: Use the Economist article Sick of work to help students understand the extent and effects of absenteeism in the workplace. They can compare the effects of absenteeism stated in the article with the effects stated in the audio story.
Reflect on the story: Take time for student reflection on the audio story and discussion questions to check for understanding. Have students think about other situations where scarcity affects the stability of a company.